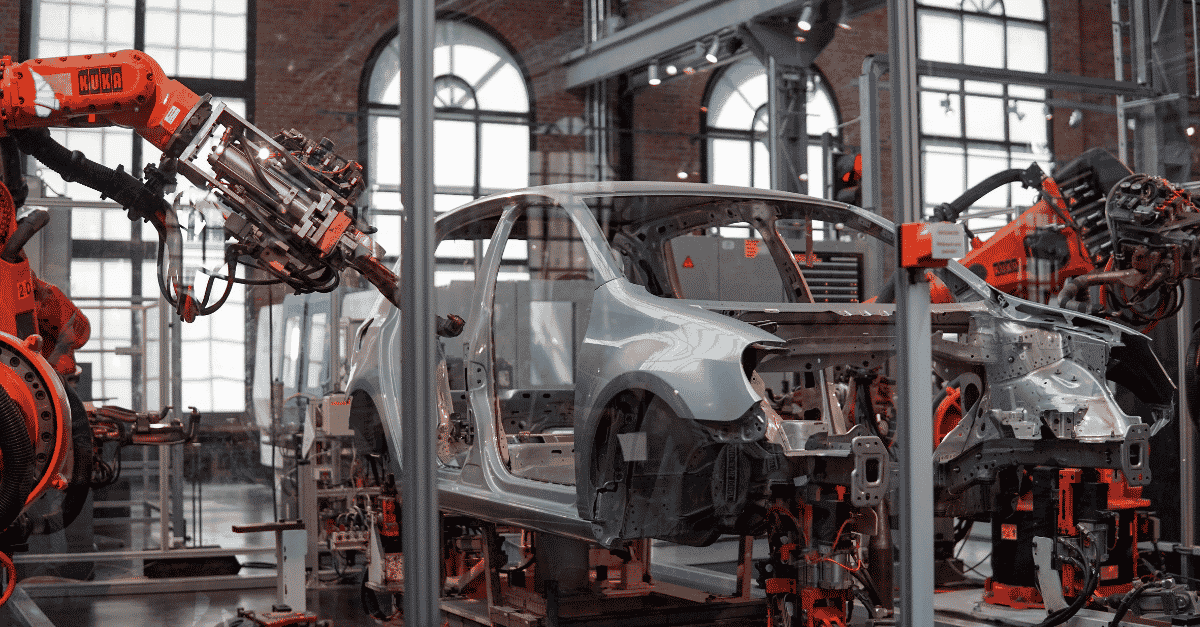
Industry Overview
The Industrial Automation industry is growing at an astounding rate. The global industrial automation market is projected to grow from USD 205.86 billion in 2022 to USD 395.09 billion by 2029, exhibiting a compound annual growth rate (CAGR) of 9.8% during the forecast period1. Industrial Automation uses control systems: robotics and computers to automate processes versus human labor. While some individuals may think this could take jobs away from the industry, quite the opposite is happening. Automation has opened up more jobs for engineers, technicians, managers, sales representatives, and customer service representatives. Robots are usually designed to carry out just one task; therefore, pairing robots with human workers is the most effective. This dynamic creates an even balance of speed & strength that robots can provide with humans’ creativity and intuition. As automation and AI technology continue to develop, automation will surge across all sectors of our society.
Types of Industrial Automation
Several types of industrial automation may be beneficial for your business based on industry and production methods. To help you make an educated decision about automation for your business, we have broken down the four most common types of automation systems below.
- Fixed/Hard Automation
Automating every step in repetitive business operations is ideal and can help improve efficiency and optimize production. Fixed automation is generally found in fixed and repetitive business operations to achieve higher production rates. It is commonly found in environments where a static assembling process is in place. An example of fixed automation would be a conveyor belt manufacturing process that moves goods from beginning to end without direct human contact (ex: food packaging).
- Programmable Automation
Programmable automation has become more popular in the last decade as technology capabilities have increased dramatically. Programmable automation is a process that runs through commands delivered by a computer program. This automation system can be found in paper mills or steel rolling mills and is commonly used to program robots in high-volume manufacturing facilities. This type of automation is more versatile than fixed automation but can’t compete with flexible automation concerning versatility. The initial costs of implementing programmable automation are very high, but the efficiency over time can increase profit margins that outweigh the initial investment costs. Programmable automation is meticulous, so it is common to use the same process for several years.
- Flexible/Soft Automation
Flexible automation allows the ability to make changes throughout the product design process. Flexible automation offers you the most versatility of the four automation processes we are highlighting. Every piece of machinery receives coded instructions from a human-powered computer enabling a wide variety of tasks to be performed by robots. A computer program still powers flexible automation, but each code is not linked together, so each machine has its own unique code (function). This type of automation system is most common in textile manufacturing (batch-process manufacturing) facilities – this type of automation is commonly used in facilities with high product varieties and low-to-medium production volume.
- Integrated Automation
Integrated automation is commonly used in advanced automation systems, specifically in the electronic and IT industries. Integrated automation systems allow the manufacturer to implement cutting-edge technologies that significantly increase efficiency and production over several years. Integrated automation is the complete automation of manufacturing plants and typically has minimal human involvement compared to the other automation processes. Integrated systems operate through a database with unique codes for each step in the process. For this process to be optimized, you will have to stay up to date with new technologies to update your system.
Each automation system is based on its integration and versatility level in the manufacturing process. Every automation system has pros and cons, and depending on your process, you may favor one method over another. There is no perfect solution to optimize manufacturing, but a system that balances human involvement and AI technology may be the best choice right now.
Advantages/Disadvantages
There are many advantages and disadvantages of industrial automation that may impact whether organizations implement automation at their facilities.
Advantages:
- Increased Production
- An excellent automation system can run diagnostics and locate bottlenecks within the production process. An optimal automation system can identify bottlenecks within a process before they significantly impact productivity. You want each step in the process to have a similar production time to optimize manufacturing. If you have one step that is much longer than another, commonly defined as “lag time,” the process cannot continue until the lengthiest step is complete.
- Better Use of Raw Materials.
- Robots and artificial intelligence aren’t perfect, but they have a lower margin of error than humans if the technology is implemented correctly. A quality production system can track the amount of material used, material waste, and production rates.
- Product Quality
- An optimized production system has the potential to improve product quality and speed up production. Product quality can be improved using automation due to the lower margin of error percentages of robots and artificial intelligence compared to humans. Automation aims to keep up to date on technology upgrades to optimize the production system.
- Safety Improvements
- Automating the production process helps keep humans safe and out of harm’s way. It can decrease the amount of unsafe work and insurance claims for human labor while increasing the number of jobs that are less of a safety risk
Disadvantages:
- Limited Technical Capabilities
- Performing complicated or non-repetitive tasks is difficult for automated systems. In the future, this will change as technology continues to advance. But right now, some processes are hard to implement, and many production facilities do not have the capital to implement these processes fully. Over time, automation will reduce labor costs and increase work quality, but the cost of implementation will still be a pain point for companies without the capital.
- High Implementation Costs
- Once automation is implemented, these costs go down, but the initial implementation costs are significant. The initial cost isn’t the only obstacle to consider. It is important to examine the potential costs of designing and building the automation process to suit your needs. Note that the lead time to design and build a machine can be drawn out from anywhere between 20 to 55 weeks on average2.
- High Variable Costs
- Human workers are the only workers capable of performing complex processes and can react in real-time to potential errors in the production process. Another huge disadvantage of industrial automation is extremely high maintenance, troubleshooting, and training costs. Your current employees will need to be trained in operating machines and maintaining the production of the automation. There are also a lot of unpredictable costs associated with industrial automation, such as research, development, and preventative maintenance.
Automation in recent years has become more prevalent and has allowed many companies to remain competitive in one of the largest industries in the world. The world has yet to see a perfect automation process. Depending on the manufacturing process, your business must decide whether automation is a good fit. It may be a good fit if you have the capital to invest in an automation system. Implementing automation slowly and combining artificial intelligence with human intelligence is the optimal way to integrate automation into your process. The industrial automation industry will continue to be more popular over the next decade – the question to ask is, will this trend influence unemployment rates?
Careers in Industrial Automation
As more companies adopt automation processes, one main concern is the extinction of production labor jobs. This should be a concern, but the argument has a flip side. For example, BMW’s Spartanburg factory features robot assistants to help fit doors with sound and moisture insulation, a painstaking task for human workers. This transition led to a 50% productivity increase without job losses, as employees previously filling these machine operator roles were promoted from machine operators to robot programmers3. While entry-level positions may be limited, there will be more opportunities for the growth of specialized roles: automation technicians, electricians, mechanical plumbers, field systems engineers, and automation engineers. These are just many of the few positions that have experienced massive demand in recent years. The career outlook for these fields is excellent, showing potential for high pay rates.
Due to industry demands, the opportunities for industrial automation will continue to multiply. The World Economic Forum estimates that by 2025, 85 million jobs may be displaced by a shift in the division of labor between humans and machines, while 97 million new roles may emerge in adaptation to this new division between humans, machines, and algorithms4. There are now classes at two-year institutions and four-year universities that allow you to get the proper training and certifications for a prosperous career in automation. In some cases, you do not even need an associate’s or bachelor’s degree if you have the required experience and technical skills. If you specialize in a specific coded language, you could set yourself apart from other candidates.
Choose NCW
In recent years, we have seen an enormous shortage of materials worldwide. The COVID-19 pandemic was undoubtedly the catalyst of this trend. But long-term outlook gives us hope that the mess we are currently in could help boost the overall stability of our domestic economy. Many companies have begun re-shoring manufacturing facilities back to North America from other countries due to supply-chain issues, increases in demand, and raw material shortages. As AI technology continues to become more prevalent in the coming years, there will be no shortage of professional roles at manufacturing facilities. As stated in a recent article by Reuters, North America laid out more than $2 billion for almost 40,000 robots in 2021 to help them contend with record demand and a pandemic-fueled labor shortage5. If companies start re-shoring manufacturing facilities back to the United States, this could increase the need for specialized professionals to fill these roles.
Our professional services recruiting teams specialize in finding talent suited for these roles. More companies have a growing demand for technical positions that require a specialized set of skills. Having the right person in every role can be transformative for an organization. Our process is designed for efficiency and accuracy, leveraging 20+ years of experience. Our team presents only the most skilled, experienced, and aligned candidates passionate about adding value to an organization. We work with your best interests in mind to make sure the right people are working in the correct positions. Do you want to optimize your manufacturing facilities? Reach out to us to find out how to get started and to find top talent in automation.
Contact Us: https://www.teamncw.com/contact-us/
Professional Services: https://www.teamncw.com/industries-served/professional-services-recruiting/
General Apply: https://jobs.teamncw.com/