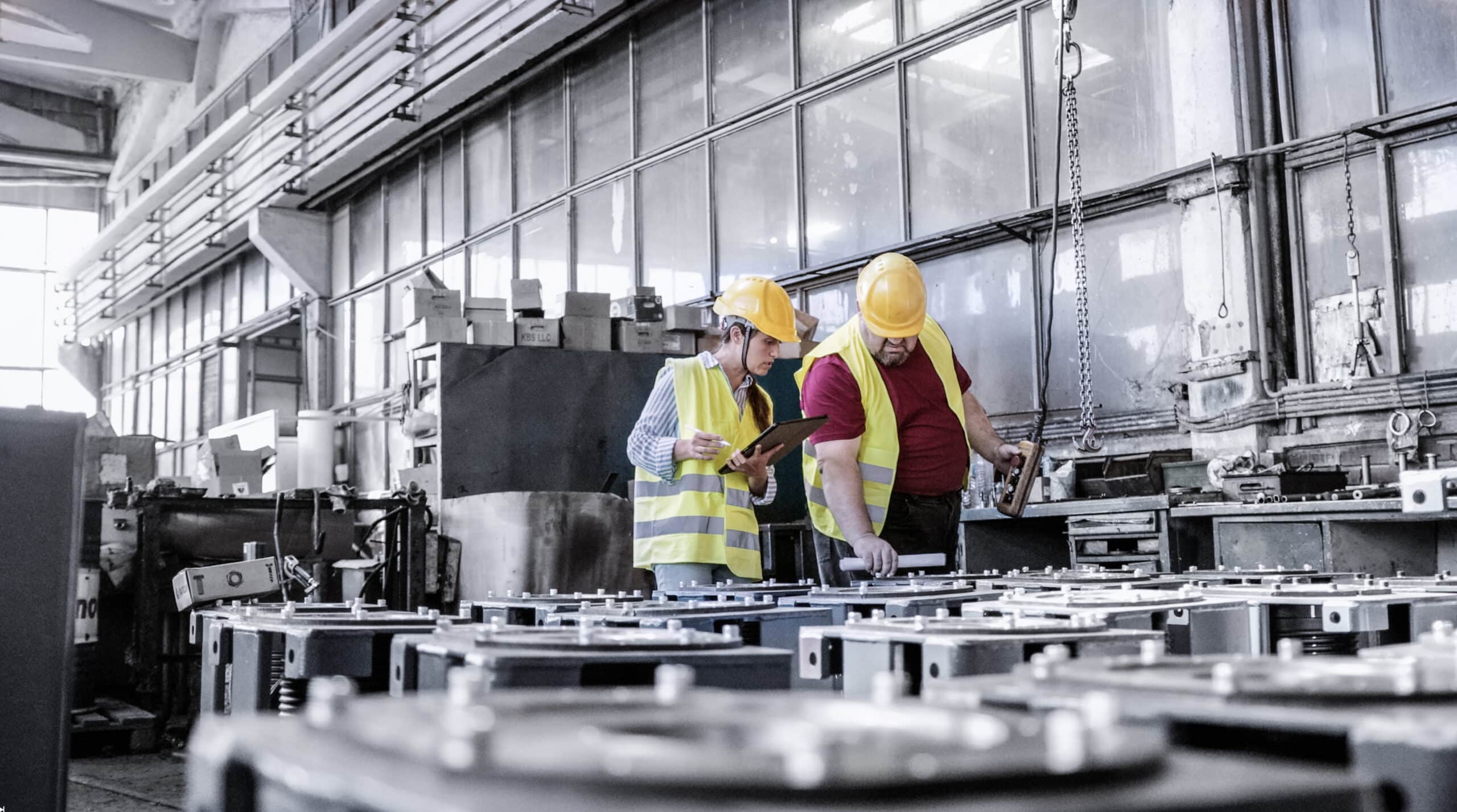
What Do Quality Assurance Technicians Do?
If you’re detail-oriented, enjoy problem-solving, and want to play a critical role in making sure products meet high expectations, a career as a quality assurance technician might be the right fit for you. These professionals, often referred to as QC technicians, are essential to manufacturing, construction, and distribution industries, ensuring that operations run smoothly and products meet quality standards and law compliance regulations.
So, what do quality assurance technicians really do on a day-to-day basis? Let’s break it down.
What the role entails
At its core, a QC technician’s job is to make sure that the products a company produces are consistent, safe, and meet all required quality standards. This could mean inspecting raw materials, testing products during various phases of production, or reviewing final outputs before they’re shipped to customers.
In many industries—especially manufacturing, construction, and warehouse operations—this role is not only vital for company success, but also for law compliance with industry regulations.
Key Responsibilities Include:
- Inspecting and testing materials, equipment, and products
- Monitoring production processes for deviations
- Recording data and maintaining inspection records
- Reporting any defects or non-conformities
- Communicating with production teams to resolve issues
- Ensuring all products adhere to company quality standards
- Verifying that procedures meet law compliance requirements
Where Do QC Technicians Work?
You’ll find quality assurance technicians in nearly every industry NCW serves. Their roles might look slightly different depending on the field:
- Manufacturing: Testing assembly line products for defects
- Construction: Reviewing materials for durability and specification alignment
- Warehouse & Distribution: Checking packaging and product conditions before shipment
- Engineering: Verifying that components meet performance and safety criteria
Each environment offers unique challenges but shares the same goal—maintaining consistent product quality and safety.
Skills and Toolsets
Successful QC technicians bring a blend of technical knowledge, observational skills, and communication abilities to the table. Some of the most in-demand skills include:
Soft Skills:
- Strong attention to detail
- Excellent problem-solving ability
- Communication and collaboration with teams
- Time management and organization
Technical Skills:
- Understanding of quality management systems (QMS)
- Familiarity with industry-specific software or tools (such as calipers, micrometers, and gauges)
- Knowledge of regulatory requirements and law compliance procedures
- Ability to interpret technical drawings and blueprints
Many companies offer on-the-job training, but having prior knowledge or certifications in quality control or manufacturing processes can be a huge plus.
Why Quality Standards and Law Compliance Matter
One of the most critical parts of a quality assurance technician’s job is ensuring that products meet all applicable quality standards and regulations. In some industries, failing to meet these requirements can result in safety issues, product recalls, or legal consequences.
For instance:
- In construction, improperly tested materials can lead to safety hazards
- In manufacturing, a defective part can shut down an entire assembly line
- In distribution, poor packaging quality can damage goods during transit
Maintaining compliance with local, state, and federal laws is not just good practice—it’s non-negotiable.
How to Become a Quality Assurance Technician
There are several ways to get started as a QC technician:
- Education: A high school diploma or GED is typically the minimum requirement. Some employers may prefer candidates with an associate degree or technical training in quality control, engineering, or manufacturing.
- Certifications: Earning certifications like the Certified Quality Technician (CQT) from the American Society for Quality (ASQ) can boost your resume.
- On-the-job training: Many companies offer training programs for entry-level candidates who show potential and a strong work ethic.
If you’re willing to learn and passionate about maintaining high standards, there’s plenty of room to grow in this field.
Career Outlook
Demand for quality assurance technicians is expected to remain steady, especially in industries where law compliance and consumer safety are top priorities. As companies continue to improve their processes and expand operations, they need reliable QC technicians to help uphold quality standards.
Experienced technicians can advance into roles like quality supervisors, quality engineers, or operations managers—making this a promising long-term career.
Ready to Start Your Career as a QC Technician?
Quality assurance technicians play a vital role in keeping companies compliant, efficient, and trusted by their customers. If you’re looking for a job that makes a tangible impact, offers career growth, and lets you work hands-on with products and processes, this could be the right path for you.
Let NCW help you take the next step. Our recruiters specialize in connecting talented candidates with top companies in manufacturing, construction, engineering, and warehouse and distribution industries. Whether you’re entry-level or experienced, we’ll help match you with a role that fits your skills and goals.
Contact NCW today to explore open positions and start your journey as a QC technician!